In the highly regulated environment of chemical manufacturing, equipment reliability and process safety are of utmost importance. Double Block and Bleed (DBB) valves have been extensively deployed in chemical processing plants to provide secure isolation, reduce leakage risks, and enhance worker and equipment safety. Their versatile design and performance reliability make them indispensable for critical operations across the chemical industry.
Understanding the Double Block and Bleed Valve Configuration
A Double Block and Bleed valve features two separate isolation mechanisms (usually ball, gate, or plug valves) and a bleed valve in between. This configuration allows for the isolation of a process stream on both the upstream and downstream sides while enabling any trapped fluid or pressure between the valves to be safely vented. The result is a highly secure seal that prevents product migration and ensures safe maintenance.
In chemical processing environments where hazardous and reactive chemicals are frequently handled, this three-valve functionality becomes a necessity, not a luxury.
Role in Enhancing Process Safety
In chemical plants, process fluids often consist of corrosive, flammable, or toxic substances. Leaks, even of minimal quantities, can lead to equipment damage, fire hazards, contamination, or health risks to workers. DBB valves are used to create a verifiable seal that isolates the system entirely, enabling maintenance or modifications to be carried out safely and without shutting down entire sections of the plant.
By venting the cavity between the block valves, the system integrity can be confirmed before personnel engage with any process line. This makes DBB valves especially vital in units dealing with acids, solvents, and polymeric compounds.
Common Applications in Chemical Facilities
DBB valves are applied across several critical areas within chemical plants:
Reactor Feed Lines: Used to isolate feed systems and prevent backflow during batch changes or catalyst replacement.
Heat Exchanger Inlets and Outlets: Deployed to ensure safe maintenance of heat exchangers without affecting upstream operations.
Instrumentation Lines: Protect sensors and analyzers from exposure during cleaning or calibration procedures.
Transfer Lines: Used during product changeover to prevent cross-contamination.
Each application benefits from the valve’s ability to provide tight shutoff, ensure zero leakage, and reduce the number of flanges and connections—consequently minimizing potential leak points.
[caption id="" align="alignnone" width="1350"]
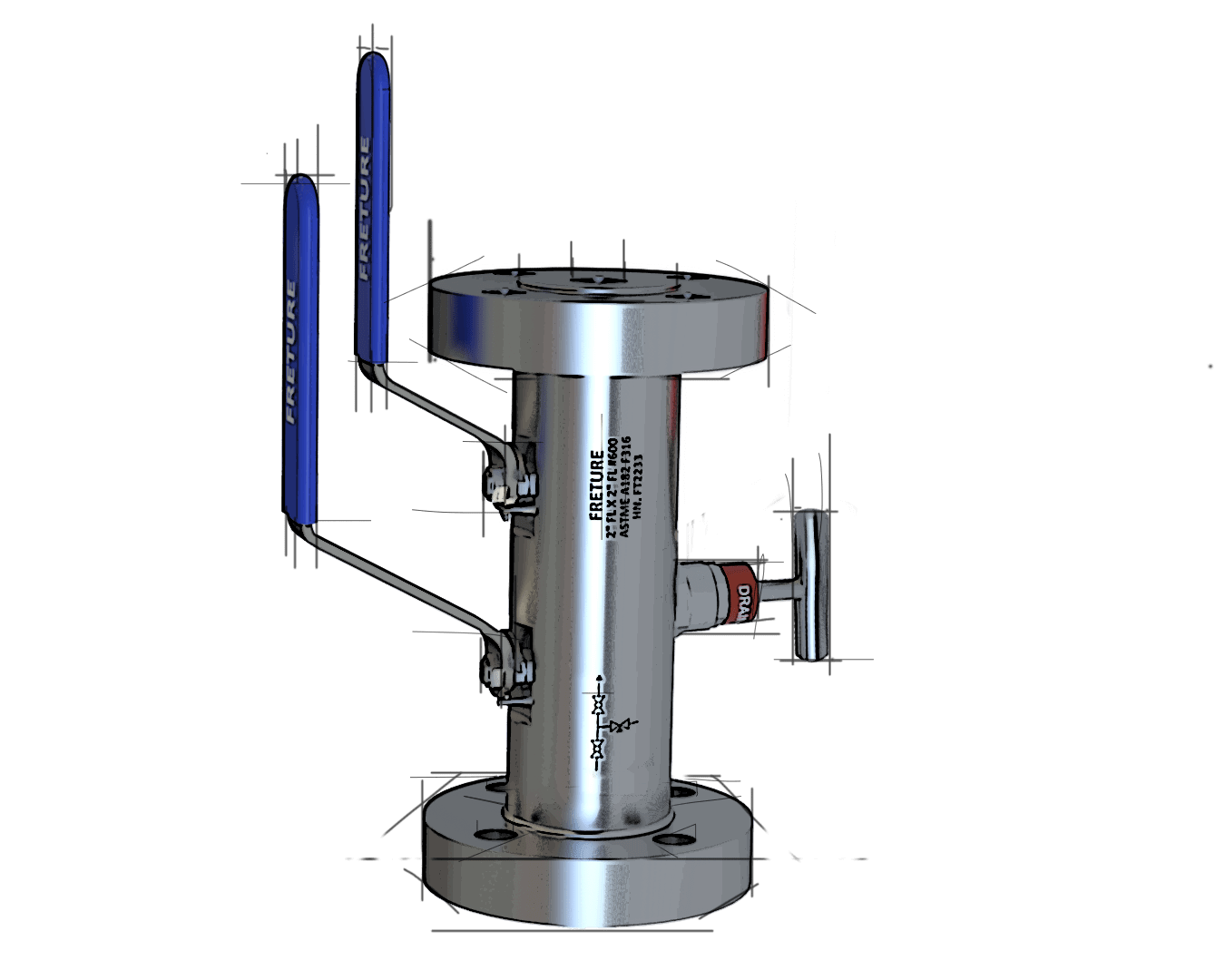
Advantages Over Traditional Valve Systems
Traditionally, two separate block valves and a bleed valve would have been installed individually to achieve double isolation. However, such setups increase the number of connection points and occupy more space. With DBB valves, these functions are combined into a compact and integrated unit.
Advantages include:
Reduced installation footprint
Minimized leak paths due to fewer joints
Simplified maintenance and fewer spares
Improved safety compliance and reduced operational downtime
These benefits align with the core goals of chemical processing—safe operation, process efficiency, and cost-effectiveness.
Compliance with Industry Standards
To meet industry requirements, DBB valves used in chemical plants are typically manufactured to comply with standards such as API 6D, ASME B16.34, and ISO 15848 (fugitive emission standards). Materials are selected based on chemical compatibility, with common body materials including stainless steel, alloy steel, Hastelloy, and Monel.
Additional certifications like ATEX and PED are often required when DBB valves are installed in explosive or pressure-regulated environments, further ensuring safety and regulatory alignment.
The deployment of Double Block and Bleed valves in chemical processing plants has become essential for maintaining safety, improving process reliability, and supporting maintenance efficiency. Their compact design, leak prevention capabilities, and ease of use make them a preferred solution for handling dangerous chemicals under stringent operating conditions.
Sourcing DBB valves from a trusted and experienced manufacturer is highly recommended to ensure the valves meet process demands and industry regulations. Investing in quality valves ultimately safeguards personnel, equipment, and the overall integrity of the chemical plant.